BASE AND COLUMN
The base and the column are built in a single cast iron Meehanite ® with oversized ribs able to withstand the most severe stresses. These are subjected to stabilization treatment outdoors for a minimum period of 6 months allowing to eliminate the remaining internal tensions; the geometry of the base has been designed to facilitate chips evacuation and operator accessibility to the machine. Base and column are designed according to the application of the analysis and design system (FEA). Using this system the computer determines the thickness and dislocation of the internal ribs. In addition to the remarkable stability the basement's body and the column are such as to guarantee a very high level of finish on any working material. On the base are made the guides for the transverse movement of the cross slide (Y axis), the work table (X axis) and the 4 augers for evacuation of chips. On the column are obtained the guides for the vertical movement of the spindle line (Z axis).
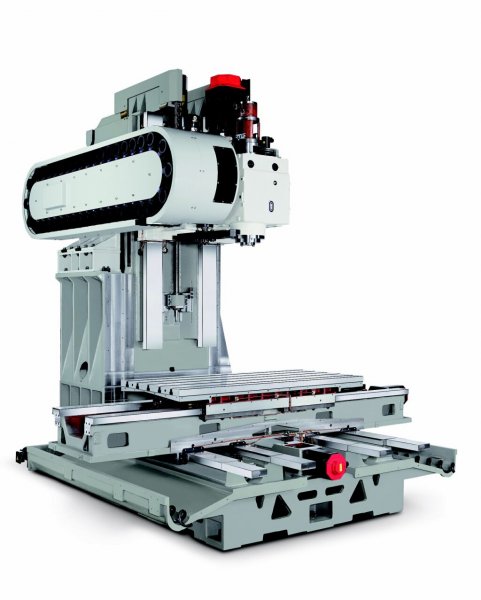
CROSS SLIDE AND WORKPIECE TABLE
The cross slide and the workpiece table are also constructed in a single cast Meehanite ® cast iron. The slide has 4 flat guides for transverse movement (Y axis) at the bottom and the two guides for sliding the workpiece table (X axis) at the top. The workpiece table has a series of "T" grooves at the top for fixing the pieces or equipment. Table surface and grooves are ground.
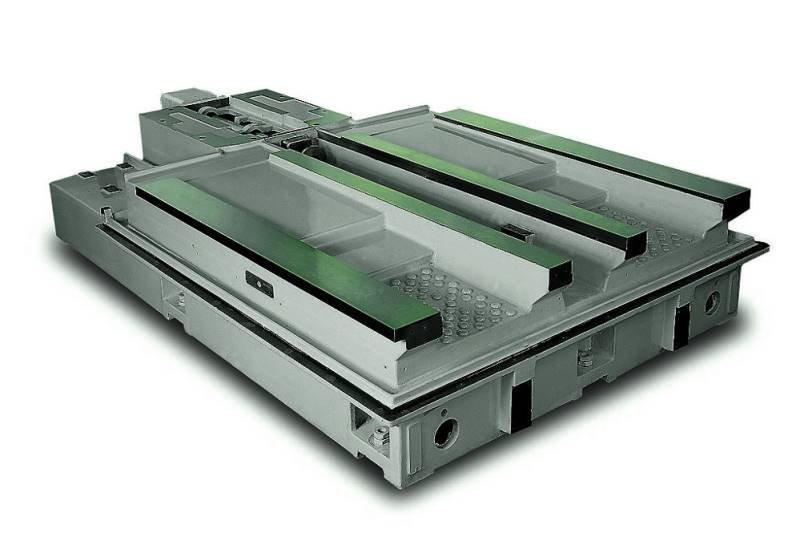
GUIDES
The three main movements of the machine (X, Y, Z) are all on flat guides through Turcite. An efficient automatic, timed forced lubrication system ensures constant lubrication on all contact surfaces. The dimensions of the guides are such as to make the specific pressure very low even under very heavy loads and stresses.The three main movements of the machine (X, Y, Z) are all on flat guides through Turcite. An efficient automatic, timed forced lubrication system ensures constant lubrication on all contact surfaces. The dimensions of the guides are such as to make the specific pressure very low even under very heavy loads and stresses.
SPINDLE LINE
It has a monolithic structure in Meehanite ® cast iron. The structure is "thermally symmetrical" to limit the effects of any temperature ranges that may be generated. An efficient cooling system with external cooling unit keeps the temperature constant. The structure of the spindle line has in the rear the two flat guides widely dimensioned for sliding on the column (Z axis). The transmission of the motion is by belt with mechanical gear box to 6.000rpm; optional it is possible to mount spindle in direct line with electronic range change to 10.000 or 12.000 rpm (in this case the spindle cone is an ISO-40). Standard is equipped with a Fanuc α15i motor (15-18,5kw); optional you can mount a more powerful Fanuc α18i motor (18,5-22kw).
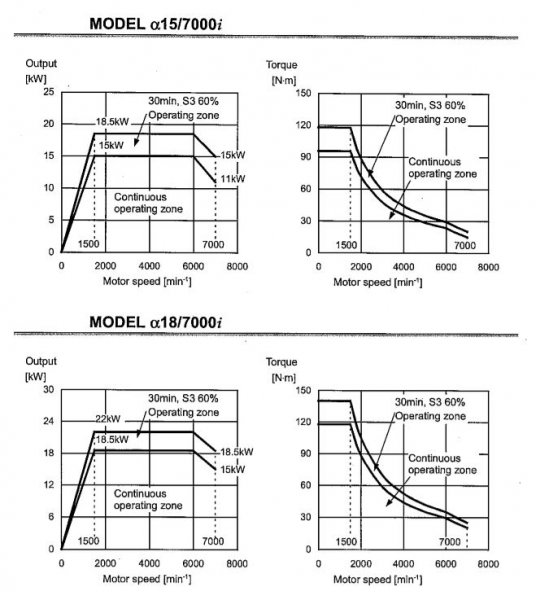
TOOL CHANGE
The automatic tool change system consists of a "chain" type magazine positioned on the right side of the column and a double-grip exchanger arm. Standard storage capacity is 24 seats. A 32 or 40-seat tool changer can be fitted as an option. The exchanger arm is built according to concepts of remarkable strength and reliability over time. The selection of the tool type "Random" bidirectional with search of the tool according to the shortest path allows a quick pre-selection during processing, then a time masked. The tool change is very fast: only 4.6 sec. (Tool to Tool) are needed to make it.
CHIP CONVEYOR (OPT.)
It’s hinged type with the drain positioned on the left side of the machine (seeing it from the front); on request you can place it on the opposite side. Its maintenance and cleaning is extremely simple and fast extracting it from the front of the machine. Carpet dimensions have been sized for a long life while having to evacuate a large amount of steel chips or other material. Included is the chip pick-up trolley also.
REFRIGERATION TOOL UNIT
It is complete with a very large collection tank capable of collecting up to 760L pump and pipes for the refrigeration of the spindle and the cleaning of the machine. On request the system is equipped with additional high pressure pumps for the passage of water through the spindle and systems for waste oil recovery in the tank to prevent pollution of emulsions.
ELECTRONIC EQUIPMENT
The system is integrated with the machine CNC and is complete with a watertight cabinet. All controls as well as the steering unit are located at the front, while the control cabinet is located at the rear of the machine. An effective air conditioning system ensures that the operating temperature inside the electrical enclosure is controlled and constant to prevent that electronic components used from being damaged, especially in warmer seasons.
PNEUMATIC SYSTEM
Complete with filter unit, reducer, lubricator and solenoid valves. This system feeds the cleaning devices of the tool connection cone on the spindle and the blowers against the ingress of foreign bodies into the spindle itself.


C.F. e P.iva 04801780281
SDI J6URRTW
info@vimak.it
0429.778060 - 0429.763525